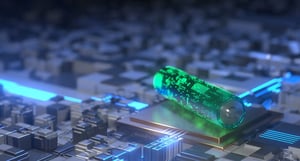
Shaping the Future of Battery Manufacturing with Digitalization
Achieve high-quality mass production in battery manufacturing with camLine’s advanced MES solution
Powering the Future: The Growing Demand for EV Batteries
The global shift towards net zero emissions has accelerated the adoption of electric vehicles (EVs), leading to a surge in demand for EV batteries that has nearly overwhelmed supply chains. Additionally, the emergence of ‘Battery-as-a-Service’ (BaaS) is revolutionizing the industry by offering quick battery swapping, encouraging wider adoption of electric vehicles.
In response, automobile companies are partnering closely with energy sectors to secure material supplies, while battery manufacturers focus on enhancing scalability, innovation, and flexibility, including the development of gigafactories, to meet the growing demand.
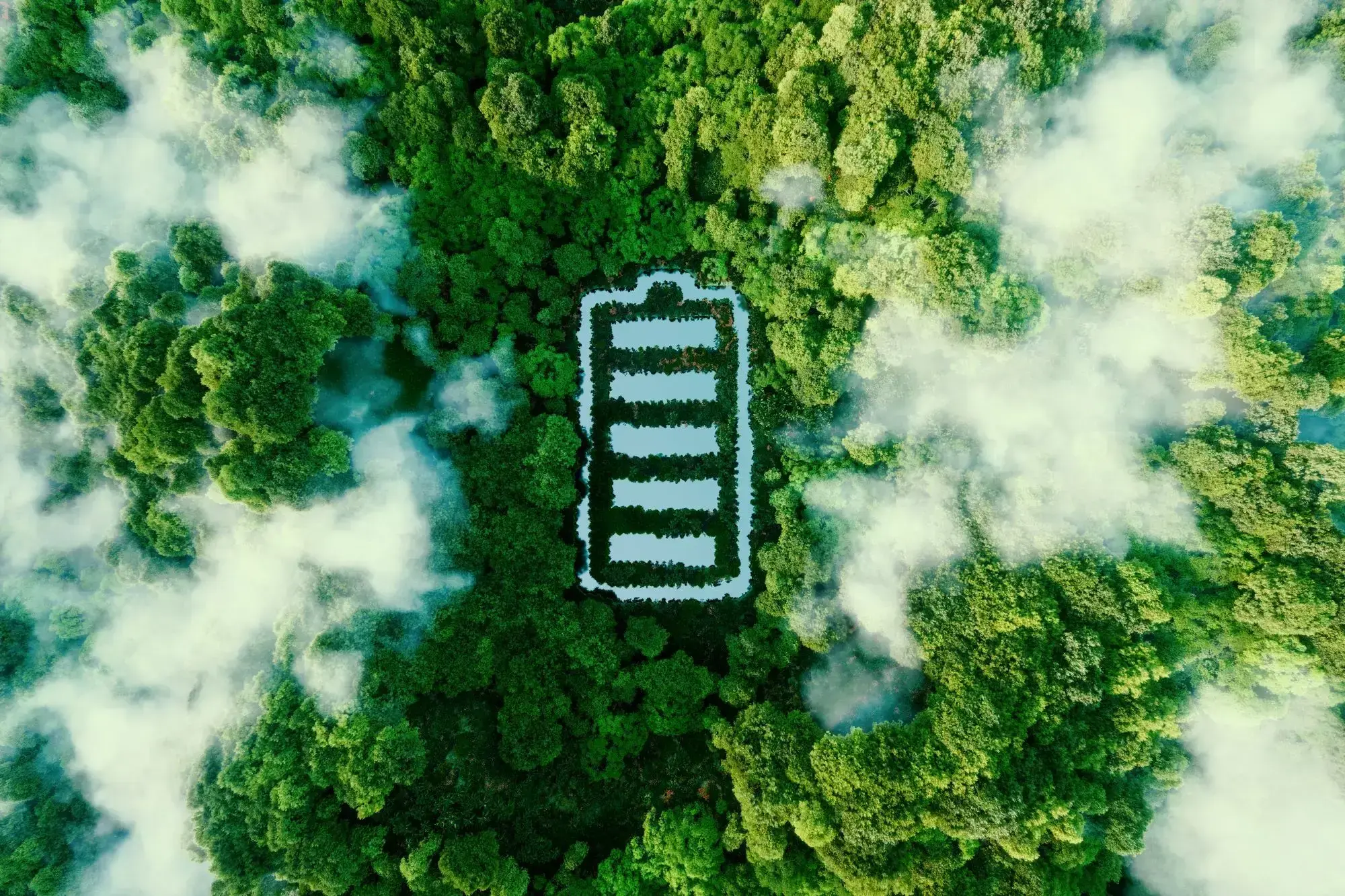
Revolutions in Battery Manufacturing
Battery manufacturers must quickly accelerate the production ramp-ups to meet rising demand. Prioritizing production efficiency and early anomaly detection is crucial to reducing production costs, boosting yields, and meeting strict delivery times. Managing large data volumes from production while achieving high-quality standards requires tight response times to ensure stable, consistently high-quality production
The Challenges
Ambitious time-to-market plans
Raw material shortage
Sustainability
Scale from lab to gigafactory
End-to-end transparency
Scarcity of knowledge workers
Quality assurance
Battery Manufacturer Needs
- Shifting from Continuous to Discrete Manufacturing
- Adapting to New Processes
- Comprehensive MES Software
- Further Requirements
The shift from continuous to discrete manufacturing in battery cell production marks a significant change in how manufacturers approach the new production process. Continuous manufacturing relies on simple MES (Manufacturing Execution System) software to ensure uninterrupted production flow, while discrete manufacturing requires more complex MES solutions.
MES software must provide real-time monitoring and detailed traceability, manage different batches and adapt to frequent scheduling and product changes to ensure that each batch meets certified quality standards while maintaining production efficiency and consistency.
Battery manufacturers must adapt to the unique challenges of discrete manufacturing, including handling production breakdown and ensuring effective batch tracking.
The MES software must support these processes with real-time monitoring, detailed traceability, and quick resolutions to ensure every batch meets manufacturing quality standards.
Battery cell manufacturers require MES software equipped with essential capabilities to meet the unique challenges of discrete manufacturing, such as:
- Enhanced Quality Control: Software for real-time inspection and monitoring are necessary to ensure that each battery cell meets industry standards for performance and safety.
- Production Flexibility: The ability to easily adapt to changes in batch sizes, configurations, and production schedules is crucial in a rapidly evolving market.
- Resource Optimization: Efficient management of materials, equipment, and labor helps reduce waste and improve productivity – a key function of MES systems.
As battery manufacturing evolves, MES software must also incorporate advanced features such as:
- Complete Traceability (from continuous and discrete manufacturing to the end product)
- Predictive Quality
- Root Cause Analysis
First-time-right production is critical, along with the implementation of a “battery passport” to track the lifecycle of each battery cell, ensuring compliance, sustainability, and transparency throughout the supply chain.
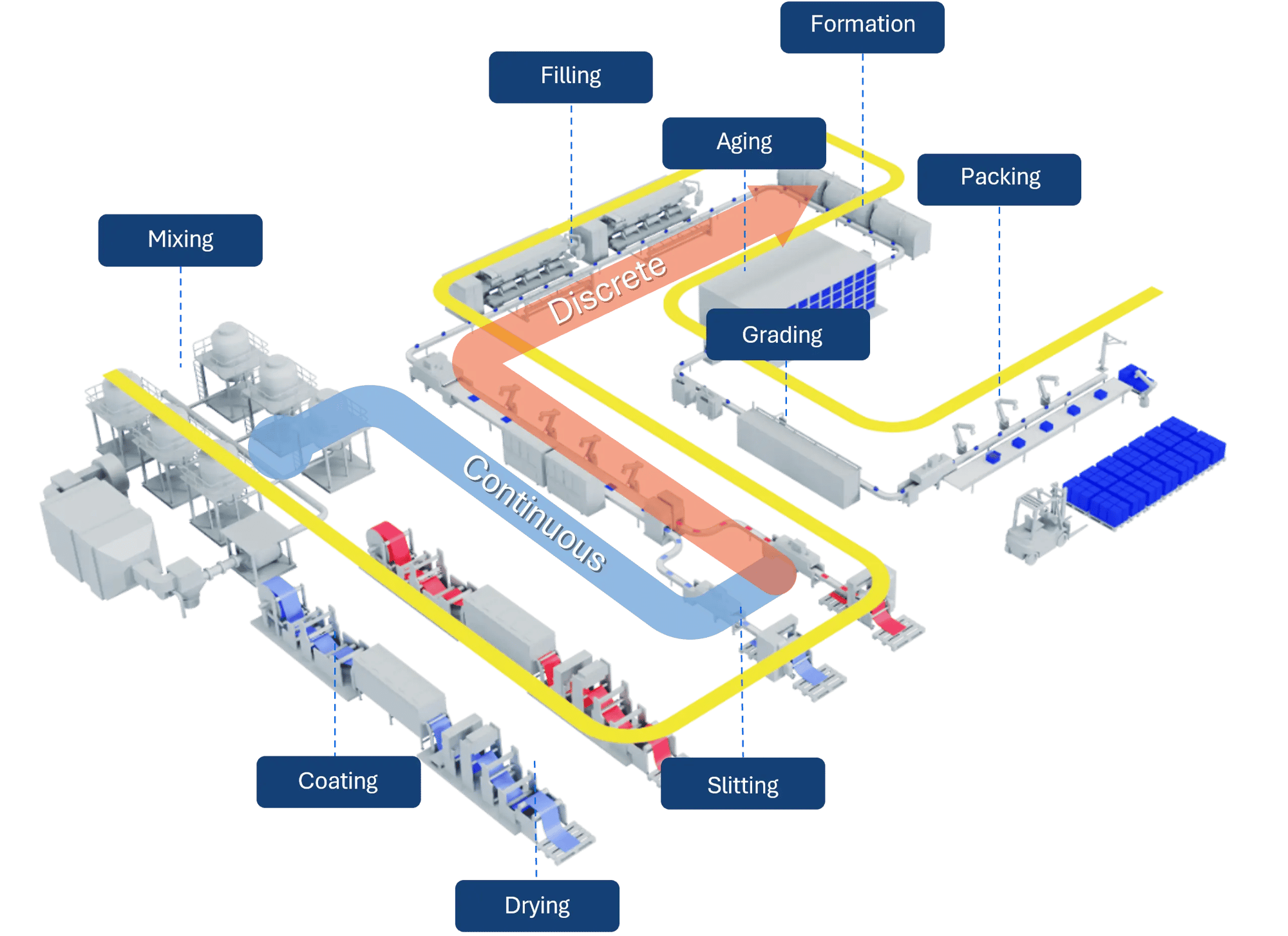
Complete Traceability
Focus on anode/cathode quality parameters with comprehensive traceability down to the individual cell layers to ensure the integrity and quality of the individual battery cells and ultimately the entire battery pack at every stage of production.
Dead Zones Identification
The identification of dead zones in the production processes of anode and cathode rolls through the precise detection of unusable roll sections is crucial for reducing waste and improving quality – even in downstream production steps.
Battery Passport Ready
From 2027, the battery passport mandates full traceability of battery packs and the seamless recording of data on the origin and composition of materials during production. Our MES supports these requirements with customized data reports that ensure compliance of the battery passport.
Collaboration with Universities and Research Institutes
camLine collaborates with universities and research institutes for battery production and integrates the latest findings into its solutions to benefit our customers.
AI/ML-Supported Data Analysis
Our AI/ML-supported data analysis add-on enables predictive classification of battery cells, accelerating production ramp-ups and boosting yields in battery manufacturing.
MES Solution for Production Quantity, Quality, and Efficiency in Battery Manufacturing
InFrame Synapse: MES Software as a Cutting Point
InFrame Synapse MES Battery Edition is the all-in-one manufacturing execution system solution for production control in battery manufacturing and high-tech fabrication sites.
A well-established MES solution ensures complete and efficient track and trace, along with overall real-time monitoring and reporting from raw materials to end products. In addition, InFrame Synapse MES Battery Edition provides data visibility at every stage of production, accelerating production ramp-ups and flow, boosting yield, and enabling anomaly detection while maintaining high production flexibility.
Core Features and Benefit
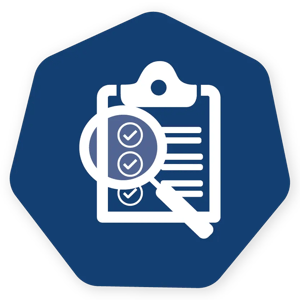
Complete product genealogy and traceability – from raw to finished goods
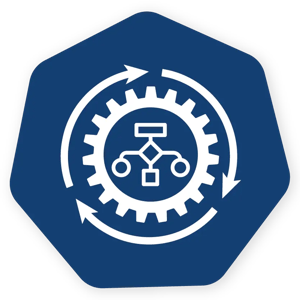
Integrated workflow engine to support different business processes
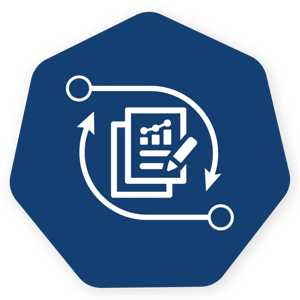
Built-in audit trails for master data and transaction data
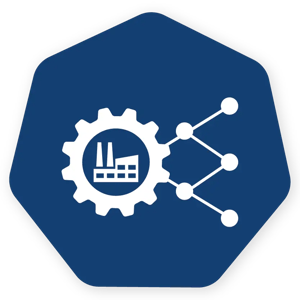
Unique industry-specific version driven by industry
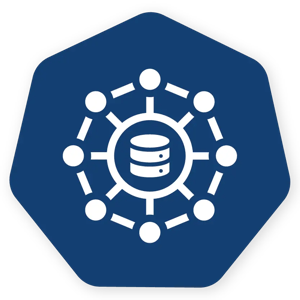
Seamless industrial standard compliance & data integrity with a best-in-class data collection framework
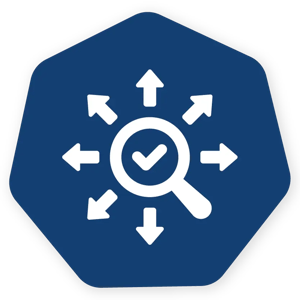
Fast and easy OpenAPI
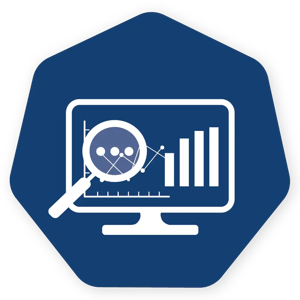
Built-in Application Performance Monitoring (APM)
InFrame Synapse MES Battery Edition: A Single Data Source Empowering All User Groups
Production Manager
Process Engineer
Plant Engineer
“Developing a continuous process is one of my tasks, and therefore I do need real-time data of the actual process in combination with product data, process plans, consumables, recipes, etc.”
Operator/Worker
Trust Us as Your Partner: Start Your Project with camLine
Customer-oriented project consulting delivers high efficiency and quality to your battery manufacturing line. We believe that our expertise will deliver the best solutions for our clients and ensure successful project implementation. The basis for your project will be provided by software solutions with out-of-the-box capabilities and high stability.
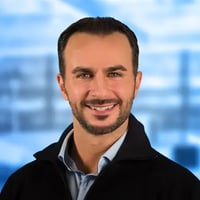
.webp?width=533&height=300&name=digital-continuity-in-battery-manufacturing-video-podcast%20(1).webp)
Collaborative Research Partnership: Digital Continuity in Battery Production
Discover the challenges and solutions in EV battery manufacturing in this video with Simon Voß from eLab der RWTH Aachen University and Bryan Ng, CEO of camLine.
This episode explores the critical role of digital continuity in battery production, discussing how camLine’s software solutions play a vital role in addressing these challenges through data integrity, traceability, and predictive quality management.
.jpg?width=421&height=300&name=battery-whitepaper-ai-drives-ramp-up-projects-and-yield-in-battery-manufacturing-1-1%20(1).jpg)
AI Drives Ramp-Up Projects and Yield in Battery Manufacturing
Explores the strategic integration of machine learning tools in the dynamic battery manufacturing market from this white paper. It delves into the advantages, such as increased efficiency, cost reduction, and distinct competitive edge manufacturers can achieve by implementing AI-driven automated root cause analysis in different ramp-up projects.
“With camLine's software solutions, you gain full control and visibility over the entire battery manufacturing process, including quality data records and the ability to track high product volumes in both continuous and discrete processes.”
Explore More Pages
Discover valuable resources—from our latest news, events, and webinars to white papers—that offer insights into manufacturing automation and innovation.
Let’s Discuss Solutions with camLine's Experts
Our team is ready to deliver tailored solutions that streamline your production, improve product quality, and maximize efficiency across your operations. Tap into camLine’s decades of expertise in digital transformation to overcome your manufacturing challenges.
“With camLine's software solutions, you gain full control and visibility over the entire battery manufacturing process, including quality data records and the ability to track high product volumes in both continuous and discrete processes.”